20 L Iron Drum Automatic Filling Machines
In the filling of liquid materials similar to the polyurethane industry in the domestic chemical industry, the semi-automatic simple filling was used in the past, with a low degree of automation and low production efficiency. At the same time, this kind of material will produce crystallization, corrosiveness and toxicity at room temperature, which will cause different degrees of harm to the human body. Some domestic enterprises with economic strength and foreign-funded enterprises gradually need to purchase automatic high-precision and high-speed filling lines. This equipment is developed under the background of the full-automatic filling transformation of polyurethane stock solution in China. In the full-automatic transformation, the automatic filling line is required to meet all the characteristics of the above materials, and the overall filling speed must be 950~1 000 barrels per hour.
The design scheme of filling machines According to the needs of the market and customers, an automatic filling production line of polyurethane sole stock solution for 20 L iron drum packaging was developed. According to the characteristics that materials can't contact with air for a long time and are easy to crystallize at room temperature, firstly, an automatic nitrogen filling device is designed in front of the filling station to ensure that the empty barrel is filled with nitrogen before filling; secondly, the filling head adopts a special double-layer structure design, the inner layer of the filling head is used for filling, and the outer layer is used for flushing nitrogen, so that the filling materials can't contact with the air; All the conveying parts except the end part of the filling head are equipped with an electric heat tracing system to ensure the constant temperature of the materials in the filling process without crystallization; The filling machine adopts a three-station design, namely, an empty barrel waiting station, a filling station and a heavy barrel discharging station, and adopts a servo transverse barrel pushing mechanism to realize the transportation of barrels among the three stations, thus improving the speed and running stability of transverse barrel pushing; Before the filling liquid enters the filling valve, a circular equal distributor is arranged to prevent the production efficiency from being affected due to the inconsistent filling speed of each filling head when filling under pressure; As this material can't stay in the tank for a long time after the production in the blending tank is completed, the filling machine also specially designed the shielding function of the filling head. When one or more filling heads fail to fill, it can be closed, which ensures continuous production when a few filling heads fail, as shown in Figure 1.
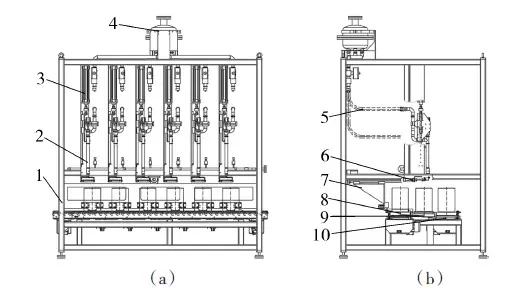
1- rack; 2- Filling head; 3- Lifting device of filling head; 4- Separating tank; 5- Metal hose; 6- Material receiving box; 7- Servo transverse barrel pushing device; 8- Empty barrel conveying line; 9- Weighing device; 10- heavy barrel outlet line
Fig.1 Structural diagram of three-station filling machine
The filling machine adopts weighing filling mode under the liquid level. In order to improve the filling speed, a three-station design is adopted, namely, an empty barrel waiting station, a filling station and a heavy barrel discharging station, and a servo transverse barrel pushing mechanism are adopted to realize the transportation of barrels among the three stations, and a series of products such as 4-10 filling stations can be developed according to the customer's output requirements. The filling machine mainly includes a frame, an empty barrel conveying device, a weighing device, a heavy barrel conveying device, a servo transverse barrel pushing device, a filling nitrogen charging system, a lifting device and a material electric heat tracing system. A closed cover door is installed outside the filling machine to ensure the cleanliness of the filling area. The filling system of the filling machine includes a liquid separation tank, a fixed seat, six liquid separation pipelines, a two-stage valve cylinder and a filling head. The liquid dispense tank is fixed at that upper end of the frame, the upper end of the six liquid dispense pipelines are communicated with the bottom of the liquid dispensing tank, and the joint of the six liquid dispensing pipelines and the liquid dispensing tank are evenly distributed on the same circumference; The center of the bottom of the liquid separation tank is in an upward convex structure, which ensures that no materials are stored at the bottom of the liquid tank; The lower end of the liquid separation pipeline is connected to the feed inlet of the filling head through a hose and a flow control valve in turn; The filling head adopts a lower-opening double-layer filling valve for filling under the liquid level. A sleeve layer is additionally arranged outside the traditional filling valve, and nitrogen can be filled into the filling head through a nitrogen pipeline. Two-stage valve-opening cylinders are arranged at the top of the filling head, so that the end valve opening has two openings, and the piston rod of the valve-opening cylinder is connected with the valve stem of the filling valve, so as to control the full opening and half opening of the filling valve. The filling speed of the liquid inlet pipeline is greater than the sum of the filling speeds of all filling valves. The electric heat tracing system of the filling machine mainly includes a heat tracing belt, terminal junction box, temperature sensor and temperature control instrument. All pipes through which materials flow are all wound around the heat tracing belt except the filling head. Each filling head is a separate heat tracing circuit, which is converged through the terminal junction box. The temperature sensor detects the actual temperature of the pipeline, and the temperature control instrument controls the on-off of the power supply of the electric heat tracing system circuit according to the comparison between the set temperature and the actual temperature, so as to ensure that the temperature of the material pipeline keeps constant at the set temperature. The lateral barrel pushing device includes a servo motor, ball screw transmission device, lateral barrel pushing frame, barrel suction device and barrel-shaped special mold. As shown in Figure 2.
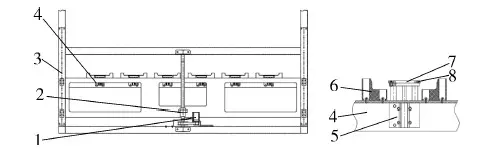
1- servo motor; 2- Ball screw rotating mechanism; 3- Servo barrel pushing device frame; 4- barrel suction device; 5- barrel suction cylinder; 6- Barrel-type special mold; 7- Magnetic bucket suction plate; 8- Magnet
Figure 2 Structure of servo transverse barrel pushing device
Fig.2 Structural diagram of servo transverse barrel pushing device
The barrel suction device is composed of a cylinder and a barrel suction plate equipped with magnets. Six barrel suction devices are installed at the front end of the horizontal barrel pushing frame, respectively facing six filling scales, and special barrel molds are installed at both ends of the barrel suction device. The magnetic barrel suction plate of the barrel suction device is not in the same plane with the mold in the normal retracted state but is a certain distance behind the mold in the horizontal barrel pushing direction, while the magnetic barrel suction plate of the barrel suction device is in the same plane with the mold in the extended state. The special mold for the barrel is matched with the barrel divider of the empty barrel conveying device to locate the position of the barrel in the direction of entering and leaving the barrel so that six empty barrels can be prepared to move transversely to the center of the weighing platform of the filling station, and at the same time, the barrel mouth is facing the filling head. Driven by a servo motor and ball screw transmission device, the horizontal barrel pushing frame drives the barrel suction device and barrels special mold to move to the empty barrel waiting station, filling station and heavy barrel conveying station, respectively. When the horizontal barrel pushing device moves to the forward direction of horizontal barrel pushing, the barrel suction device first extends out, and when moving to the empty barrel station, six-barrel molds are stuck on both sides of six empty barrels, while the magnetic barrel suction plate of the barrel suction device sucks the barrel side, and when moving forward, Only six empty barrels touch the corresponding filled heavy barrels on six scales in the filling station, driving the heavy barrels to move forward. When the six heavy barrels are moved into the heavy barrel conveying station, the servo transverse barrel pushing device stops moving forward and starts moving backward, so that the heavy barrels are separated from the empty barrels, and the heavy barrels stay in the heavy barrel conveying station and are conveyed out of the filling machine, while the empty barrels continue to move backward driven by the magnetic barrel suction plate of the barrel suction device. When the empty barrels move to the center of the weighing station in the filling station, Stop moving backward. At this time, the magnetic bucket suction plate of the bucket suction device retracts. Under the positioning of the special bucket mold, the empty bucket is separated from the bucket suction device. When the servo transverse bucket pushing device continues to move backward, the empty bucket stays on the weighing platform of the filling station and performs the filling action. Finally, the servo transverse bucket pushing device moves to the initial position. At this time, the empty bucket station can continue to feed the bucket for the next cycle. The complete working process of the filling machine is as follows: First, the empty barrels after nitrogen flushing enter the empty barrel waiting for the station in turn, and the barrels are automatically separated at equal distances by the barrel divider, which respectively corresponds to the center of the filling station scale. The servo barrel pushing device starts to move the empty barrels towards the filling station, and at the same time pushes the heavy barrels that have been filled in the filling station to the heavy barrel discharging station. At this time, the servo barrel pushing device moves backward and pulls the empty barrels back to the center of the filling station scale. At this time, the servo barrel pushing device is separated from the empty barrels. Continue to move back to the original position, and the empty barrel station is ready to feed the barrel in the next beat. When the servo barrel pushing device and the empty barrel are moved back to the filling station, the heavy barrel conveying line starts to output the heavy barrel to the filling machine. When the servo barrel pushing device is separated from the empty barrel and moves back, the filling head is inserted under the drive of the lifting device to start filling, and the filling is divided into two steps, namely, volume and flow. During the filling process, the filling head is controlled to rise gradually to ensure that the liquid level is always filled. At the same time, the outer layer of the filling head is filled with nitrogen to ensure the materials.
Control system design
Hardware design of control system
The control scheme is shown in Figure 3.
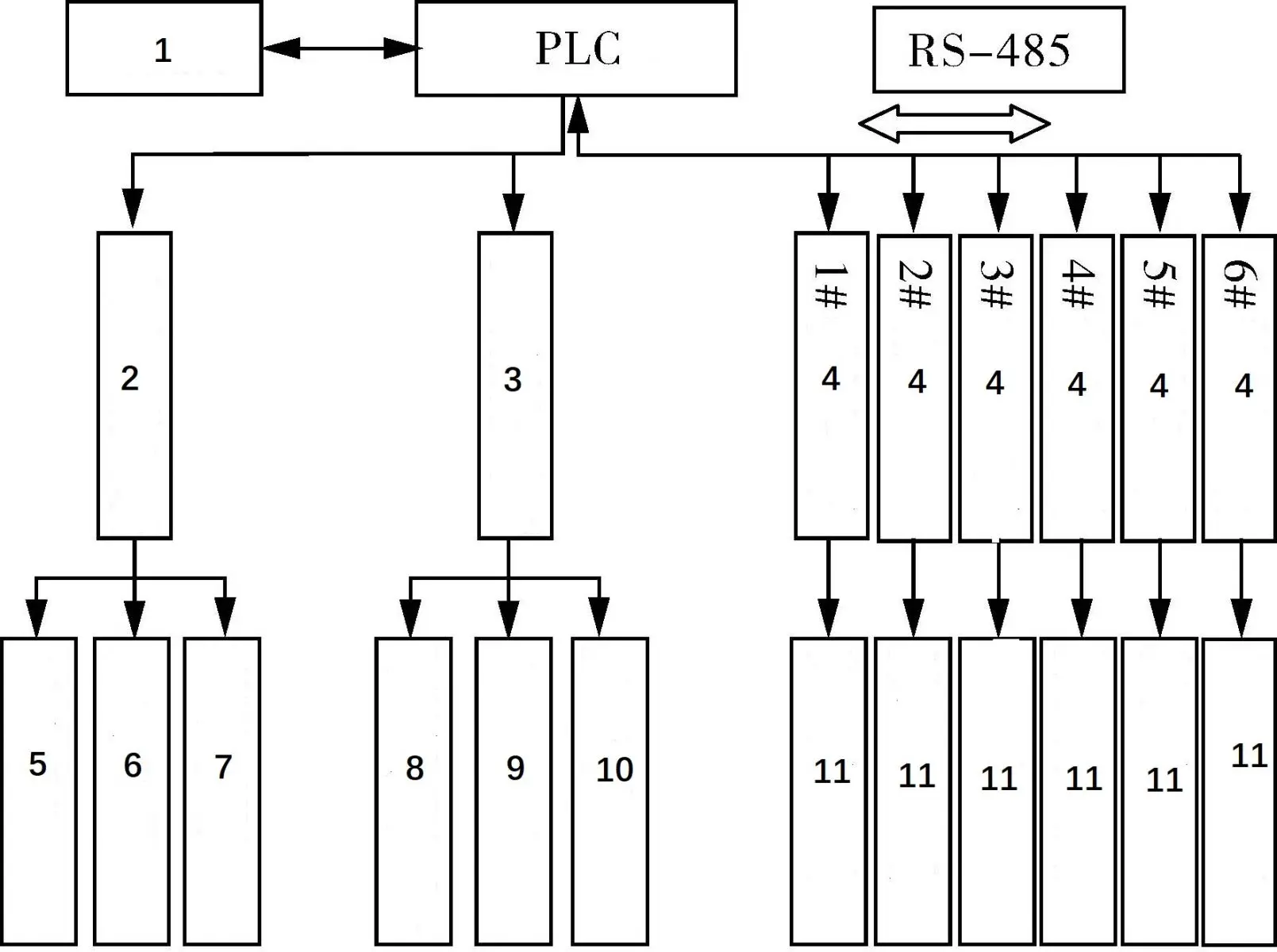
1. Automatic operation 2. Initialization 3. Three-station empty barrel feeding 4. Filling parameters downloaded to weighing instrument 5. Servo barrel shifting to filling station 6. Filling head inserted down and filling started 7. Real-time weight data of electronic scale read 8. The weighing instrument monitored filling accuracy 9. Filling 10. Filling weight qualified 11. Servo barrel shifting to barrel discharging station 12. End 13. Stop running.
Fig.3 Schematic diagram of the control scheme
The control system uses PLC as the control unit, the touch screen as the man-machine interface, the filling and weighing part is controlled by the weighing instrument, and the weighing instrument communicates with PLC through RS-485 to realize the communication of weight data and control instructions. The position control module of PLC sends the position instruction to the servo driver to realize the control of the three-position servo dialing mechanism. The closed-loop control of the constant temperature heating unit is realized by PLC, temperature control instrument and temperature sensor, and the constant temperature heating control of the filling pipeline is realized.
Control system software design The software design adopts a modular structure design, which is divided according to the functional realization of the production line, mainly including an empty barrel conveying line control program, three-station servo barrel shifting control program, weighing and filling control program, constant temperature heating control program, etc. The overall software flow is shown in Figure 4.
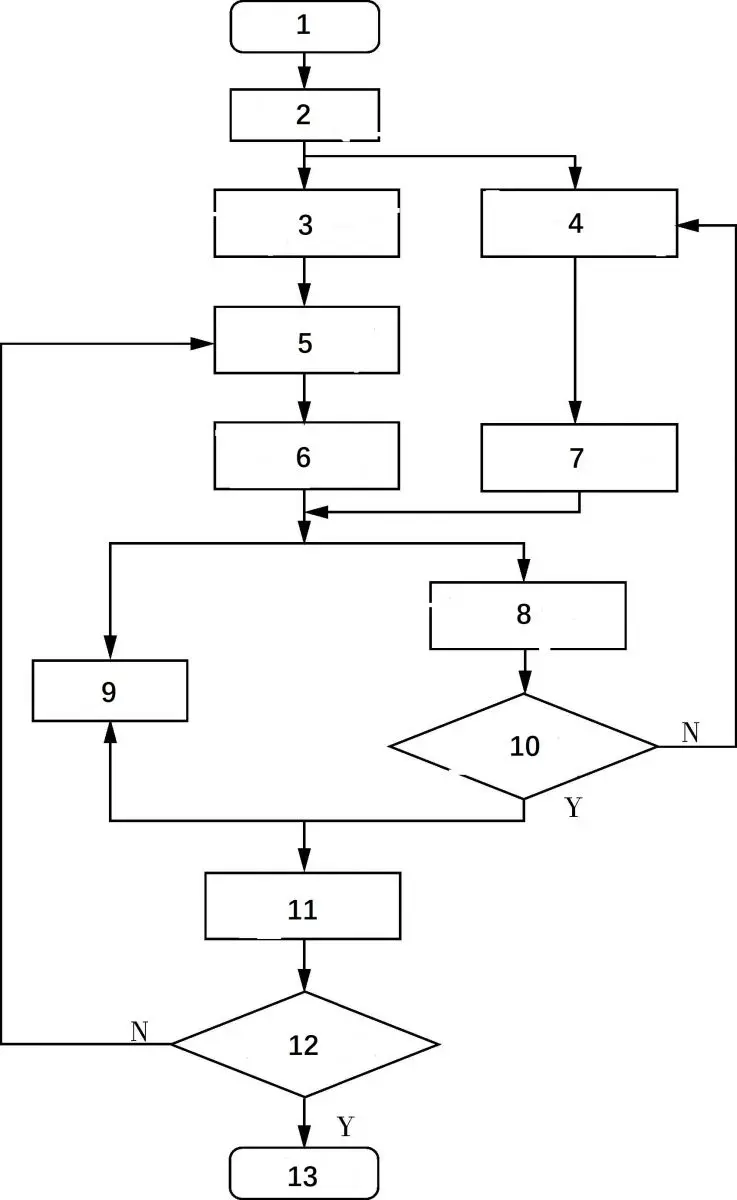
1. Touch screen 2. Constant-temperature heating unit 3. Servo barrel-shifting unit 4. Weighing instrument 5. Electric tracing belt 6. Temperature sensor 7. Temperature control instrument 8. Servo barrel-shifting motor 9. barrel-shifting mechanism 10. barrel-sucking cylinder 11. Weighing sensor
Fig.4 Flow chart of the program
After the automatic operation of the system starts, all parameters are initialized first, and the closing value of the large and small flows is downloaded into the weighing instrument at the same time as the empty barrel conveying station starts to feed. The weighing instrument will automatically control the opening and closing of the large and small flow valves according to the received values, and the servo barrel shifting mechanism will push the prepared empty barrels transversely to the filling station to start filling. After the filling is finished, the servo barrel shifting mechanism will push the newly prepared empty barrels together with the filled heavy barrels to the barrel discharging station, and then return the empty barrels to the filling station for the next filling, and the system will be updated.
Conclusion The packaging line absorbs the respective advantages of existing filling machines for chemical products at home and abroad and has the advantages of high precision, high speed, high automation and convenient operation. Mainly has the following advantages:
(1) Three-station design of filling machine is adopted, barrel feeding, barrel filling and barrel discharging are carried out in parallel, and the horizontal barrel shifting device is driven by a servo motor, which reduces the filling cycle beat and improves the running speed and stability; It is the same 6-head 20 L filling machine. The filling speed of the traditional linear filling machine is about 600~700 barrels /h, while that of the three-station filling machine is 950~1 000 barrels /h, and the overall running speed is increased by nearly 40%.
(2) The filling valve adopts a double-layer design, the inner layer is filled with materials, the outer layer is filled with nitrogen, and the upper surface of the materials is filled with nitrogen at the same time, which solves the problem that the upper liquid surface of the materials contacts with the air during filling, effectively prevents the materials from deteriorating, and provides a good solution for filling the same type of industrial materials that cannot contact with the air, and has a good popularization value.
(3) Compared with the traditional vibrating type capping machine, the capping lifting mechanism designed by the automatic capping machine based on the principle that the center of gravity changes when the caps are vertically lifted in front and back is simpler in structure, and the capping speed is greatly improved, which has a high popularization significance. Since the successful research and development, the product runs stably, has been well received by customers, and has a good market prospect. At present, it has been sold to a domestic chemical plant for a total of more than ten sets. The annual output has been greatly increased, the labor cost has been reduced, the use effect is good, the labor productivity has been improved, the labor intensity has been reduced, and it has been well received by customers. At the same time, the product has improved brand awareness and influence in the packaging industry and created considerable economic benefits.