Finite Element Analysis of Can Filling Machine Frame
The frame is an important part of the can filling machine, which bears a large load and needs high enough strength and diamond. If the local stress is too high, the structure will be destroyed, and too much deformation will affect the installation accuracy, thus affecting the filling accuracy. In this paper, based on Ansys Workbench, the frame is analyzed by the finite element method. The results show that the maximum stress of the original frame is 71.8MPa, which is less than the yield strength of stainless steel. The maximum deformation is 0.894mm, with large deformation and insufficient rigidity. After optimizing the position and structure of the frame leg, the maximum stress of the frame is reduced to 36.7MPa, which is reduced by 48.8%. The maximum displacement is reduced to 0.279mm, which is 68.8% lower than that before optimization. The strength and stiffness meet the design requirements.
The frame of the can filling machine is a permanent part of the filling machine and an important basic supporting part. It is equipped with a transmission system, a filling system, a can conveying system and a protection part. In order to ensure the safety, stability and filling accuracy of the rack, the strength, stiffness and stability of the rack are required. YLGD60 Can Filling Machine developed by Hefei Zhongchen Light Industry Machinery Co., Ltd. is 60-head high-speed equipment. The finite element method is used to analyze the frame, and according to the analysis results, the number, position and part of the structure of the support legs are improved and optimized again, which provides a reference for the structural design of the frame.
Structure of can-filling machines As shown in Figure 1, the filling machine consists of the transmission system, tank conveying system, a filling system, a protective door and a frame. The transmission system provides power for the whole filling machine; The can conveying system is responsible for outputting the filled cans from the filling system; The filling system fills the liquid into the cans according to the set parameters. Comprises a frame bedplate and supporting legs, wherein the bedplate is supported by the supporting legs and is provided with a transmission system, a filling system, a tank conveying system and a protective door.
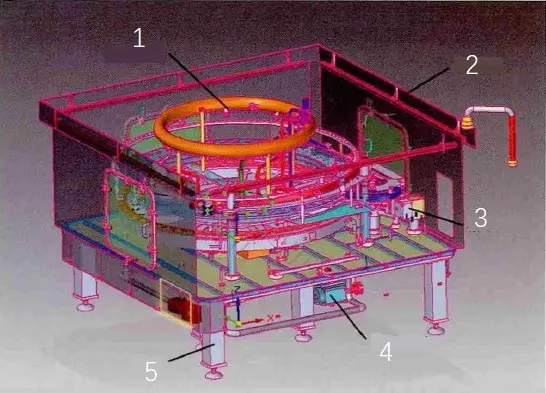
Fig. 1 Structure of can filling machine
1. Filling system 2. Protective door 3. Tank conveying system 4. The transmission system 5. Frame
Establish analysis model Establish the model of the rack in Workbench. In DesignModeler, the establishment surface is the bedplate, which is divided into the connection support surface between the bedplate and each component. The reinforcing ribs and legs on the platform are represented by straight lines according to the positions and sizes in the three-dimensional model. As shown in Figure 2.
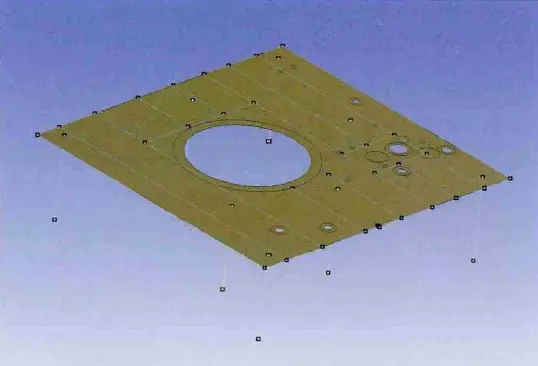
Figure 2 Rack model
Set and analyze parameters 1. Parameter setting and grid division
The slab material and reinforcing ribs are 304 stainless steel, and the density is 7.93X103kg/m3, the elastic modulus is 195GPa and Poisson's ratio is 0.3 as defined in the material properties. The material of the leg is Q235, and the density defined in the material property is 7.85X103kg/m3.
The elastic modulus is 210GPa and Poisson's ratio is 0.33. The plate grid adopts a shell unit, with a thickness of 35mm and made of 304 stainless steel; The reinforcing ribs are set as beam units and made of 304 stainless steel; The legs are set as beam units, made of Q235, and the grid sizes are all set to 10mm. After grid division, it is shown in Figure 3. Each beam element and shell element are rigidly connected to coordinate the deformation of the whole model.
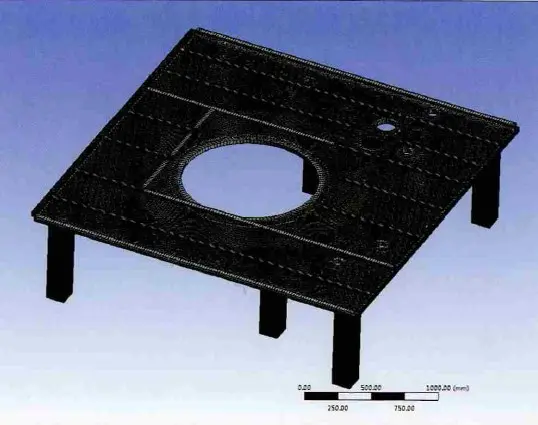
Figure 3 Rack Grid
2. Boundary conditions
The weight of the filling system is about 3060kg, and the force in the -Z direction is 30,000 N at A; The weight of the two transition wheels is about 35KG, and the force in the -Z direction is applied respectively, which is about 343 N; The weight of the wheel is about 76.8KG, and the force in the -Z direction is about 753.5n; The bottle conveying line weighs about 32Kg, and exerts a force in the -Z direction, about 313.6n; The bottle feeding screw weighs 46Kg and exerts a force in the -Z direction, which is about 450 N; The load at the lifting post of the cam is about 44.9KG, and the force in the -Z direction is about 440N, totally two places; The load at the column of the tank system is about 32kg, and the force in the -Z direction is about 313.6N, totally four places; The turbine box weighs about 200kg, and is suspended under the bedplate by four upright posts, and the four upright posts are respectively loaded with a force of 490N in the -Z direction; Protective devices are installed around the platform, each weight is about 150Kg, and the force in the -Z direction is about 1470N. Full restraint is applied to the legs. After the load and constraint are applied, it is shown in Figure 4.
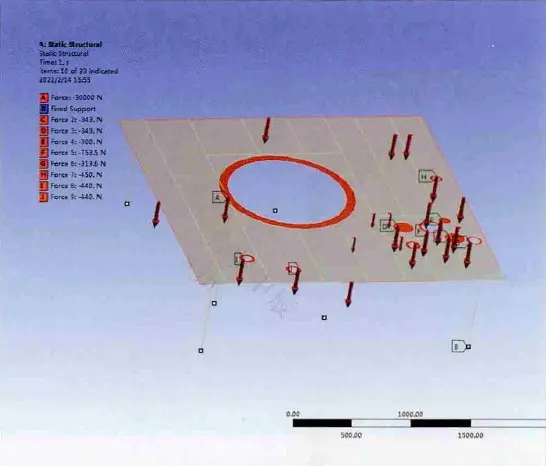
Figure 4 Load and constraint diagram
3. Analysis results
Through finite element analysis and calculation, the stress distribution and displacement program of the frame are obtained. It can be seen from Figure 5 that the maximum stress of the frame is 71.8MPa, less than 210MPa, which meets the working requirements of the bedplate. The maximum stress position is shown in the figure. The maximum deformation is 0.894mm, and the position is shown in Figure 6. Due to the 1m-long column installed on the bedplate, the deformation is too large; The deformation at the protective door is obvious, and the supporting strength cannot meet the design requirements.
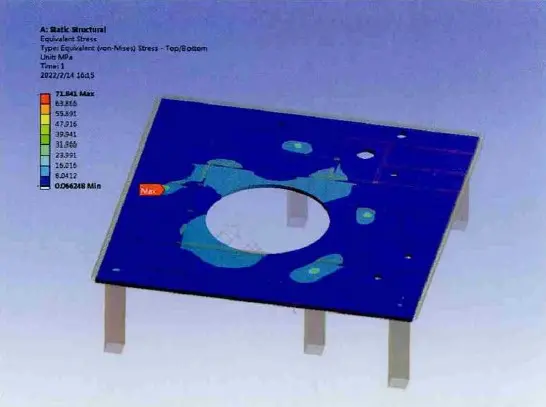
Fig. 5 stress nephogram
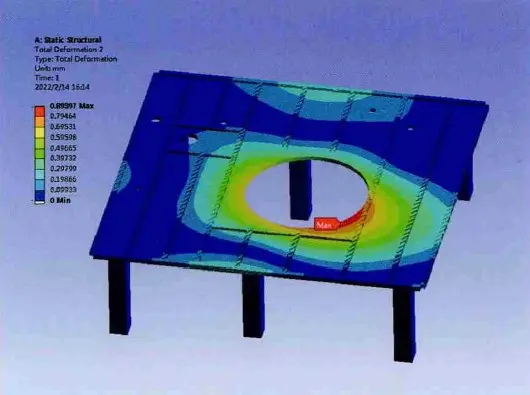
Fig. 6 Displacement nephogram
Structure optimization After analysis, the filling system has the largest deformation at the installation place, and the middle three legs are slightly thin, so adjusting the position can't improve the overall stiffness and strength. Add a leg near the position with the maximum deformation and adjust the positions of the other legs; In order to reduce the deformation at the place where the protective device is installed, reinforcing ribs are added around the edge of the bedplate, and the optimized structure has meshed as shown in Figure 7.
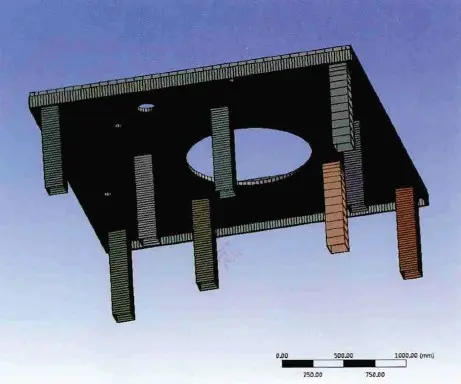
Figure 7 Grid diagram after structure optimization
Re-apply the constraint and load, and get the displacement nephogram and stress nephogram through analysis and calculation. It can be seen from the figure that the maximum stress is reduced to 36.7MPa, which is 48.8% lower than before. The maximum stress position is shown in Figure 8. The maximum displacement is reduced to 0.279mm, which is 68.8% lower than that before optimization. The maximum position is shown in Figure 9.
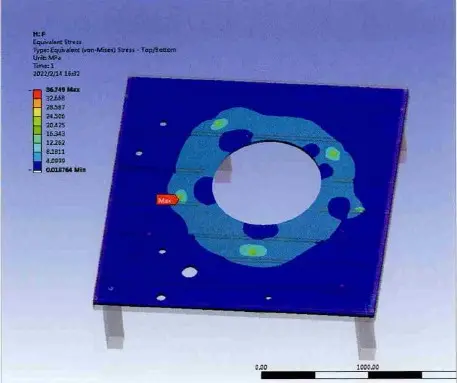
Fig. 8 optimized stress diagram
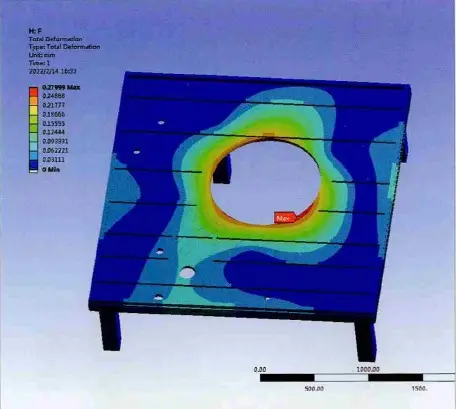
Fig. 9 optimized displacement diagram
Conclusion After analyzing and optimizing the structure, the stress and deformation are greatly reduced, which meets the design requirements. Subsequent practice shows that the deformation of the frame is obviously reduced, the installation accuracy is improved, and the workload and difficulty of debugging are reduced.